For Compliance Managers, an OSHA surprise inspection is where strategic governance meets operational reality. The inspector’s questions, sampling methods, and document requests test not only safety performance but the strength of your compliance management system – policies, controls, and evidence trails.
This paper translates the latest OSHA guidance (2024-2025) into an action‑oriented playbook so compliance leaders can steer the organization through an inspection with composure, data integrity, and minimal business disruption.
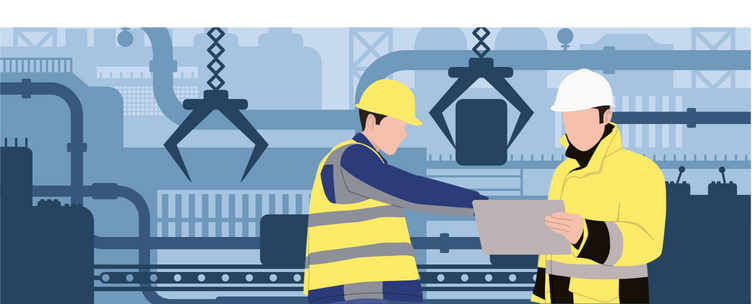
Why Your Facility Lands on the Inspection List
OSHA assigns resources by statutory priority, but programmed inspections – driven by National, Regional, or Local Emphasis Programs (NEPs, REPs, LEPs) – now account for a growing share of visits, especially in warehousing, distribution, and high‑hazard sectors. For example, NEP CPL 03‑00‑026 targets facilities with elevated musculoskeletal, forklift, and heat‑stress risks (OSHA, 2023).
Compliance takeaway: Maintain a “regulatory trigger map” that aligns each active emphasis program to your NAICS codes. Update quarterly so you can pre‑position evidence (e.g., ergonomic assessments) before OSHA knocks.
Opening Conference – Set Scope & Governance
The opening conference isn’t just a formality – it’s your first line of defense. When an OSHA inspector arrives, your Compliance Manager plays a critical role in setting the tone and establishing the ground rules. This isn’t the moment for guesswork. From verifying credentials to defining the inspection’s scope and designating escorts, each step is guided by OSHA’s own playbook – including new updates like the 2024 Worker Walkaround Rule.
The Compliance Manager should attend the opening conference to:
- Authenticate credentials and confirm the inspection’s legal basis.
- Clarify scope against OSHA’s Field Operations Manual (FOM) criteria; request a warrant only if scope exceeds the stated trigger (OSHA, n.d.).
- Assign escorts – one management, one employee. Under the 2024 Worker Walkaround Rule, employees may also choose a qualified third‑party rep; prepare visitor protocols that protect proprietary data.
Document Control: Your First Line of Defense

Most Cited Violations: A Predictive Risk Lens
Workplace safety is no guessing game – and when OSHA shows up, your compliance strategy shouldn’t be either. Every year, thousands of employers get tripped up by the same hazards, earning themselves costly citations and avoidable headaches. Below is a snapshot of the top 10 violations for FY 2024 – aka your compliance cheat sheet (OSHA, 2024):
- Fall protection – 29 CFR 1926.501
- Hazard communication – 1910.1200
- Lockout/Tag‑out – 1910.147
- Ladders – 1926.1053
- Respiratory protection – 1910.134
- Powered industrial trucks – 1910.178
- Fall‑protection training – 1926.503
- Scaffolding – 1926.451
- Eye/face protection – 1926.102
- Machine guarding – 1910.212
Preventive tip: Use this list as an internal audit checklist at least quarterly.
The Walkaround: Evidence Over Eloquence
Inspectors will take photographs, conduct interviews, and collect samples. As Compliance Manager:
- Chain‑of‑custody parity: Request splits of industrial‑hygiene samples and mirror OSHA’s labeling conventions.
- Real‑time documentation: Log all inspector observations and questions to reconcile later with the closing‑conference notes.
- Interview consistency: Provide the inspector a list of trained personnel but do not coach employees; instead, rely on demonstrable training records.
Penalty Exposure & Cost-Benefit Decisions
Compliance isn’t just about safety – it’s also about strategy. When a citation hits your inbox, you’ve got 15 working days to make a critical call: contest, conference, or comply. And with OSHA’s 2025 inflation-adjusted penalties reaching as high as $165,514 per violation, that decision can carry serious financial weight – especially for repeat offenses (OSHA, 2025). Smart employers weigh the cost of abatement against the risks of escalation. Here’s a breakdown of the numbers and a few key questions to guide your next move:

Post-Inspection Governance Cycle
Day 0–3: Assemble the inspection file and draft a gap analysis against internal standards (e.g., ISO 45001, ISO 37301).
Day 4–10: Implement immediate abatement actions; capture photo evidence.
Day 15: File Notice of Contest or attend the informal conference.
Day 30+: Integrate lessons‑learned into policy revisions, audit protocols, and management‑review meetings.
Continuous Improvement for Compliance Leaders
Compliance isn’t a one-and-done; it’s an ongoing strategy. Staying ahead of OSHA (and avoiding repeat violations) means moving from reactive fixes to proactive systems. That’s where next-level compliance tools and habits come into play. From quarterly horizon scans to integrated audits and airtight documentation, the goal is simple: build a culture of safety that’s visible, verifiable, and inspector-ready. Here are four proven practices that help organizations not just survive inspections – but thrive between them:
- Quarterly regulatory horizon scans: Track rulemakings, emphasis programs, and penalty adjustments.
- Integrated audit program: Blend OSHA requirements with other frameworks (EPA, DOT, ISO) to avoid siloed checks.
- Digital evidence management: Leverage EHS platforms with time‑stamped uploads and immutable logs—critical for proving due diligence during repeat‑citation disputes.
- Culture metrics: Monitor near‑miss reporting and corrective‑action closure rates; inspectors often ask for evidence of employee engagement.
Conclusion
An unexpected OSHA visit need not derail operations or budgets. When Compliance Managers align document control, risk assessment, and cross‑functional communication with current OSHA guidance, a surprise inspection becomes a live demonstration of governance in action. Preparation grounded in accurate data – and supported by a repeatable post‑inspection process – turns regulatory scrutiny into a catalyst for stronger safety performance and organizational credibility.
Download the Whitepaper
Sources
- American Psychological Association. (2024). 2023 Work in America™ Survey. https://www.apa.org/pubs/reports/work-in-america/2023-workplace-health-well-being
- Harvard Business Review. (2023, April 5). Engaged employees create better customer experiences. https://hbr.org/2023/04/engaged-employees-create-better-customer-experiences
- Occupational Safety and Health Administration. (2025, January 7). 2025 annual adjustments to OSHA civil penalties. https://www.osha.gov/memos/2025-01-07/2025-annual-adjustments-osha-civil-penalties
- Occupational Safety and Health Administration. (2024, April 1). Worker walkaround representative designation process: Final rule. https://www.osha.gov/worker-walkaround/final-rule
- Occupational Safety and Health Administration. (2024). Top 10 most frequently cited standards, FY 2024. https://www.osha.gov/top10citedstandards/
- Occupational Safety and Health Administration. (2023, June 14). National Emphasis Program on warehousing and distribution center operations (CPL 03‑00‑026). https://www.osha.gov/sites/default/files/enforcement/directives/CPL_03-00-026.pdf
- Occupational Safety and Health Administration. (n.d.). 29 CFR 1904.33: Retention and updating. https://www.osha.gov/laws-regs/regulations/standardnumber/1904/1904.33
- Sanders, B. (2024, Dec.). Senate report alleges Amazon rejected warehouse safety recommendations due to productivity concerns. AP News. https://apnews.com/article/eb5b72dd501be0bcce9d919c34731290
- Seyfarth Shaw LLP. (2022, Nov 29). OSHA citation liability 2023—Don’t lose the forest for the trees. https://www.seyfarth.com/news-insights/osha-citation-liability-2023-dont-lose-the-forest-for-the-trees.html
- Wang, Y., & Verma, V. (2024). Nothing to fear: Strong corporate culture and workplace safety. Journal of Financial Services Research. https://link.springer.com/article/10.1007/s11156-024-01264-6
- SHRM Research Institute. (2024). 2023‑24 State of the Workplace Report. https://www.shrm.org/content/dam/en/shrm/research/2023-2024-State-of-the-Workplace-Report.pdf