When a Compliance Safety & Health Officer (CSHO) walks through the gate without notice, the OHS team – not HR – becomes the front line. From programmed National Emphasis Program (NEP) inspections to unprogrammed visits after a complaint, successful outcomes depend on technical readiness: defensible sampling plans, meticulous logs, and confident command of inspection protocol. This paper distills the latest OSHA guidance (2024-2025) into a pragmatic playbook so OHS officers can turn a surprise visit into a structured demonstration of due diligence rather than a six‑figure liability.
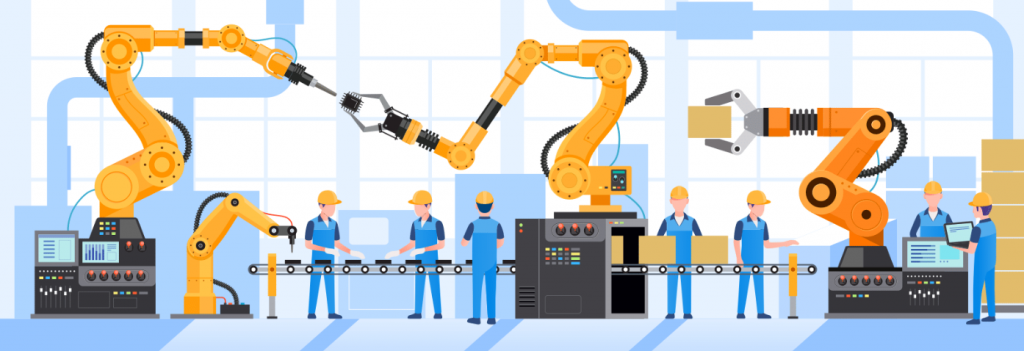
How Your Site Gets on OSHA’s Radar
OSHA still follows the classic priority ladder – imminent danger, fatality/catastrophe, complaints, then programmed inspections – but recent emphasis programs are tilting the odds toward high‑hazard sectors such as warehousing and distribution (OSHA, 2024).
Action item: Map any active NEPs, REPs, or LEPs to your NAICS codes and keep the justification file handy; CSHOs often open with “Tell me how you manage the hazards targeted by NEP CPL 03‑00‑026.”
Opening Conference: Set the Legal and Technical Boundaries
- Verify the CSHO’s credentials and scope; request a warrant only if the proposed scope exceeds the trigger.
- Designate a management escort (you) and a knowledgeable employee rep. Under the 2024 Worker Walkaround rule, employees may invite a qualified third‑party expert; plan an orientation protocol so external reps don’t slow down sampling or photography (OSHA, 2024).
- Confirm whether industrial hygiene sampling is expected. If so, request split samples and document chain‑of‑custody on the spot.
Walkaround Strategy for OHS Professionals

Top 10 Citations – Root Cause, Not Just Regulations
Workplace safety is no guessing game – and when OSHA shows up, your compliance strategy shouldn’t be either. Every year, thousands of employers get tripped up by the same hazards, earning themselves costly citations and avoidable headaches. Whether you’re in construction, manufacturing, or healthcare, understanding the most frequently cited OSHA standards can help you stay one step ahead. Below is a snapshot of the top 10 violations for FY 2024 – aka your compliance cheat sheet:
- Fall protection – 29 CFR 1926.501
- Hazard communication – 1910.1200
- Lockout/Tag‑out – 1910.147
- Ladders – 1926.1053
- Respiratory protection – 1910.134
- Powered industrial trucks – 1910.178
- Fall‑protection training – 1926.503
- Scaffolding – 1926.451
- Eye/face protection – 1926.102
- Machine guarding – 1910.212
Preventive tip: Use this list as an internal audit checklist at least quarterly.
Record Keeping Hot Spots
- OSHA 300/301/300A must be retained and update‑ready for five years (OSHA, n.d.).
- Keep sampling data, calibration certificates, and SDSs in a single digital repository with field access; CSHOs increasingly ask to view documents during the walkaround rather than at closing.
- Create an “inspection binder” (physical or electronic) with: current written programs, last five years of logs, results of any NEP‑related audits, and your respiratory protection medical clearance roster.
Industrial Hygiene & Sampling Tactics
Draft your sampling plan before the CSHO arrives. The OSHA Technical Manual recommends pre‑assembling cassettes, charging pumps, and documenting calibration data in the OIS worksheet (OHSA, n.d.).
Pro tips:
- Chain‑of‑custody: use tamper‑evident seals (OSHA‑21) to match CSHO rigor.
- Duplicate sampling: request employer splits or provide your own media for parallel samples.
- Environmental log: record temperature, barometric pressure, and process changes; these data often become your defense if OSHA’s lab values appear skewed.
Penalties
OSHA’s January 7, 2025 inflation memo sets the figures that will appear on your citation. Knowing the ceiling helps you weigh whether to contest, informally settle, or invest in rapid abatement (OSHA, 2025).

Closing Conference and Beyond
Immediate abatement evidence: show photos or service tickets for any quick fixes executed during the inspection.
15‑day tactical calendar:
Day 1–3 - Assemble the inspection file, flag potential misclassifications.
Day 4–10 - Conduct an internal root‑cause analysis aligning with ISO 45001 corrective‑action clauses.
Day 15 - File notice of contest or schedule the informal conference.
Prevent “repeat” status: integrate citation items into your risk register and communicate changes to supervisors within 30 days.
- Calendar the due dates in the citation (abatement & contest periods).
- Fix quick‑hit hazards immediately – it shows good faith if penalties are later negotiated.
- Draft the abatement certification letter with photos/receipts.
- Consider an informal conference within 15 working days to seek reclassification or penalty reduction.
- Update your written programs so the same citation doesn’t become “repeat” (10× higher fine) next time (Tynan, 2025).

Continuous Improvement Loop for OHS Officers
- Quarterly NEP drills: Simulate an inspection targeting the active emphasis program for your sector.
- Sampling competency check: Rotate team members through pump calibration and media prep to reduce single‑point failure.
- Data integrity audits: Verify that incident rates, exposure data, and corrective actions reconcile across EHS software, OSHA logs, and training records.
- Stakeholder debrief: Translate technical findings into plain‑language tool‑box talks; workforce engagement is still the inspector’s litmus test for a “living” safety program.
Conclusion
Surprise inspections are not won with charm but with verifiable data, disciplined sampling, and visible worker engagement. By internalizing OSHA’s latest rules – especially the 2024 worker‑walkaround provisions and 2025 penalty tables – OHS officers can transform an unannounced visit into a showcase of proactive risk management rather than a reactive scramble.
Download the Whitepaper
Sources
- Occupational Safety and Health Administration. (2025, January 7). 2025 annual adjustments to OSHA civil penalties. https://www.osha.gov/memos/2025-01-07/2025-annual-adjustments-osha-civil-penalties
- Occupational Safety and Health Administration. (2024, April 1). Worker walkaround representative designation process: Final rule. https://www.osha.gov/laws-regs/federalregister/2024-04-01
- Occupational Safety and Health Administration. (2024). Field Operations Manual, Chapter 2: Program planning. https://www.osha.gov/fom/chapter-2
- Occupational Safety and Health Administration. (2023, July 13). National Emphasis Program on warehousing and distribution center operations (CPL 03‑00‑026). https://www.osha.gov/enforcement/directives/cpl-03-00-026
- Occupational Safety and Health Administration. (2024). Top 10 most frequently cited standards, FY 2024. https://www.osha.gov/top10citedstandards/
- Occupational Safety and Health Administration. (n.d.). OSHA Technical Manual (OTM) Section II, Chapter 1: Sampling procedures. https://www.osha.gov/otm/section-2-health-hazards/chapter-1
- Occupational Safety and Health Administration. (n.d.). 29 CFR 1904.33: Retention and updating. https://www.osha.gov/laws-regs/regulations/standardnumber/1904/1904.33